精密配件的鑄造工藝有哪些?
精密配件,指裝配機(jī)械的零件或部件;或損壞后重新安裝上的零件或部件。配件可以分為兩類:標(biāo)準(zhǔn)配件和可選配件;今天我們來講一講各種精密配件的鑄造工藝。
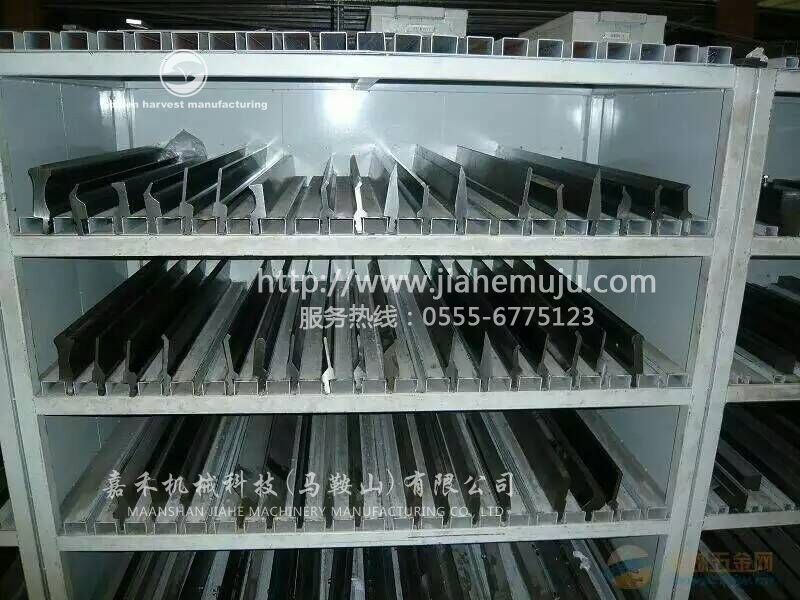
一、精密塑性成形
精密塑性加工技術(shù)在工業(yè)發(fā)達(dá)國(guó)家受到高度重視,并投入大量資金優(yōu)先發(fā)展。70年代美國(guó)空軍主持制訂“鍛造工藝現(xiàn)代化計(jì)劃”,目的是使鍛造這一重要工藝實(shí)現(xiàn)現(xiàn)代化,更多地使用CAD/CAM,使新鍛件的制造周期減少75%。1992年,美國(guó)國(guó)防部提出了“軍用關(guān)鍵技術(shù)清單”,其中包含了等壓成型工藝、數(shù)控計(jì)算機(jī)控制旋壓、塑變和剪切成形機(jī)械、超塑成型/擴(kuò)散連接工藝、液壓延伸成型工藝等精密塑性成型工藝。此外,國(guó)外近年來還發(fā)展了以航空航天產(chǎn)品為應(yīng)用對(duì)象的“大型模鍛件的鍛造及葉片精鍛工藝”、“快速凝固粉末層壓工藝”、“大型復(fù)雜結(jié)構(gòu)件強(qiáng)力旋壓成型工藝”、“難變形材料超塑成形工藝”、“先進(jìn)材料(如金屬基復(fù)合材料、陶瓷基復(fù)合材料等)成形工藝''等。近來,隨著計(jì)算機(jī)和自動(dòng)化技術(shù)對(duì)熱加工成形工藝的滲透,板材成形柔性制造系統(tǒng)也開始嶄露頭角。
二.超塑成形
美國(guó)休斯公司、 BAE公司等在超塑成形技術(shù)方面居世界前列。目前欽合金超塑成形工藝已廣泛用于制造導(dǎo)彈外殼,推進(jìn)劑儲(chǔ)箱,整流罩、球形氣瓶、波紋板及發(fā)動(dòng)機(jī)部件等。鋁合金、鎂合金、鎳基高溫合金、金屬基復(fù)合材料等的超塑成形工藝也在研究。我國(guó)的超塑成形技術(shù)在航天航空及機(jī)械行業(yè)已有應(yīng)用,如航天工業(yè)中的衛(wèi)星部件、導(dǎo)彈和火箭氣瓶等,并采用超塑成形法制造偵察衛(wèi)星的欽合金回收艙。與此同時(shí),還基本上掌握了鋅、銅、鋁、欽合金的超塑成形工藝,最小成形厚度可達(dá)0.3mm,形狀也較復(fù)雜。但壁厚均勻性問題尚待解決。
三.強(qiáng)力旋壓
美國(guó)利用強(qiáng)力旋壓精密配件技術(shù)。已能生產(chǎn)直徑為3.9m、徑向尺寸精度0.05mm、表面粗糙度Ra0.16—0.32μm、壁厚差<0.03mm的導(dǎo)彈殼體。幾乎對(duì)各種金屬均能旋壓成形,且工藝穩(wěn)定,并已實(shí)現(xiàn)設(shè)備大型化,多用途化和自動(dòng)化。錯(cuò)距旋壓、CNC等先進(jìn)旋壓工藝及設(shè)備也已普及使用。
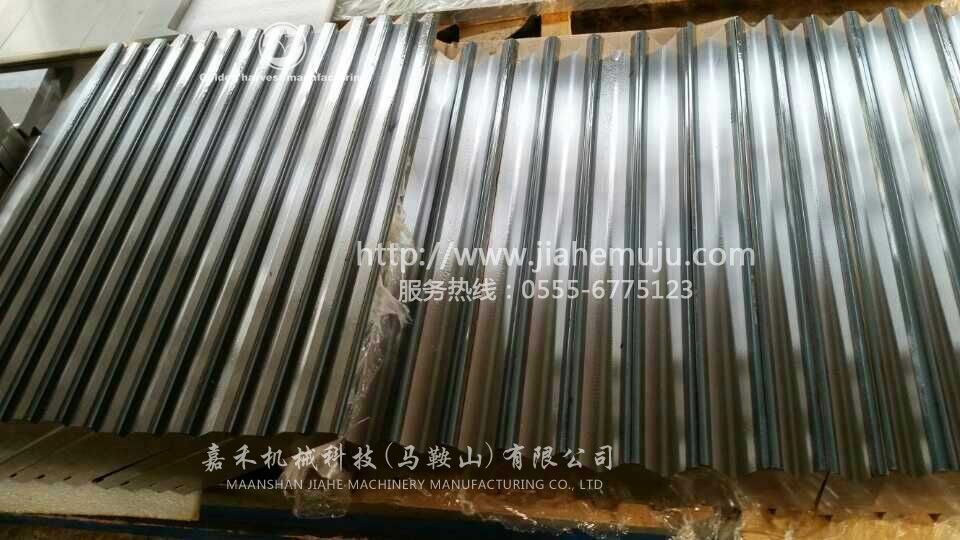
四、精密鑄造
精密鑄造成形工藝不但可以縮短新型武器的研制周期、降低成本,還可以提高武器的靈活性、可靠性。如美國(guó)波音公司生產(chǎn)的巡航導(dǎo)彈的艙體采用鋁合金精密鑄造工藝后,彈體成本降低30%,每枚導(dǎo)彈所需工時(shí)從8000小時(shí)減少到5500小時(shí),且可靠性提高,重量有所降低。
美國(guó)橡樹嶺國(guó)家實(shí)驗(yàn)室、美國(guó)精密鑄造公司和NASA劉易斯研究中心等單位對(duì)A1系金屬間化合物和Ti、
Ni基等特種合金的精密鑄造進(jìn)行了大量研究。他們采用整體一次成形精鑄工藝加工渦噴、渦扇導(dǎo)向器,減少機(jī)加工時(shí)40%,成本降低30%。我國(guó)軍工系統(tǒng)的精密鑄造工藝與國(guó)外相比差距較大。如導(dǎo)彈艙體主要采用低、差壓鑄造法。普通粘土砂鑄型生產(chǎn)艙段,尺寸精度低,表面質(zhì)量較差,內(nèi)部缺陷多,合金液二次氧化嚴(yán)重,力學(xué)性能不高,廢品率高達(dá)20%-30%,目前國(guó)內(nèi)僅能鑄造1.4m以下的艙段。另外象導(dǎo)彈尾翼、飛機(jī)部分器件等仍采用機(jī)械加工方法,不但生產(chǎn)周期長(zhǎng)、成本高,而且可靠性也較差。在特種合金精密鑄造工藝方面,同樣存在很大差距,象單品空心無余量葉片精鑄工藝,在國(guó)外已應(yīng)用于軍工生產(chǎn),而國(guó)內(nèi)尚處于研究階段。至于A1系金屬間化合物的精密鑄造工藝的研究目前還未開。 綜上所述,與國(guó)外相比,我國(guó)在精密鑄造工藝方面約落后10-15年。為了縮短新型武器的研制和生產(chǎn)周期、降低成本、提高可靠性,必須加強(qiáng)精密鑄造工藝的研究。
由于我國(guó)汽車配件制造行業(yè)起步晚、起點(diǎn)低、產(chǎn)業(yè)結(jié)構(gòu)不合理。改革開放以來,汽車配件制造行業(yè)雖有了較快發(fā)展,但與汽車生產(chǎn)大國(guó)相比,差距仍然明顯。特別是與國(guó)外配件制造企業(yè)相比,差距更為明顯。我國(guó)汽車配件制造行業(yè)的差距,除了規(guī)模上的差距,更重要的是制造技術(shù)以及管理技術(shù)上的差距;馬鞍山嘉禾機(jī)械科技有限公司專業(yè)從事折彎模具,數(shù)控折彎模具,生產(chǎn)線配件,精密配件,模具/配件加工,優(yōu)良的設(shè)備,精湛的工藝,嚴(yán)格的檢驗(yàn),完善的售后服務(wù).聯(lián)系電話:18005552119
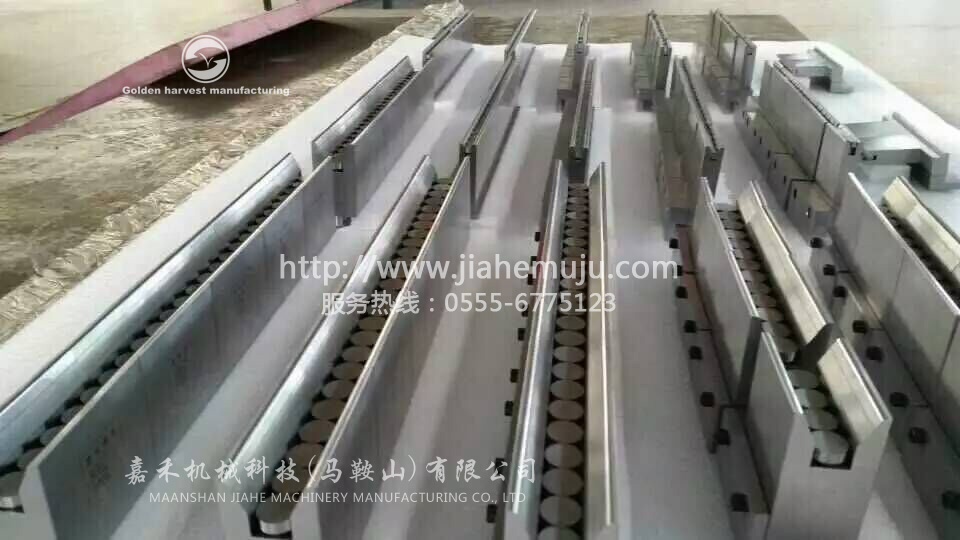
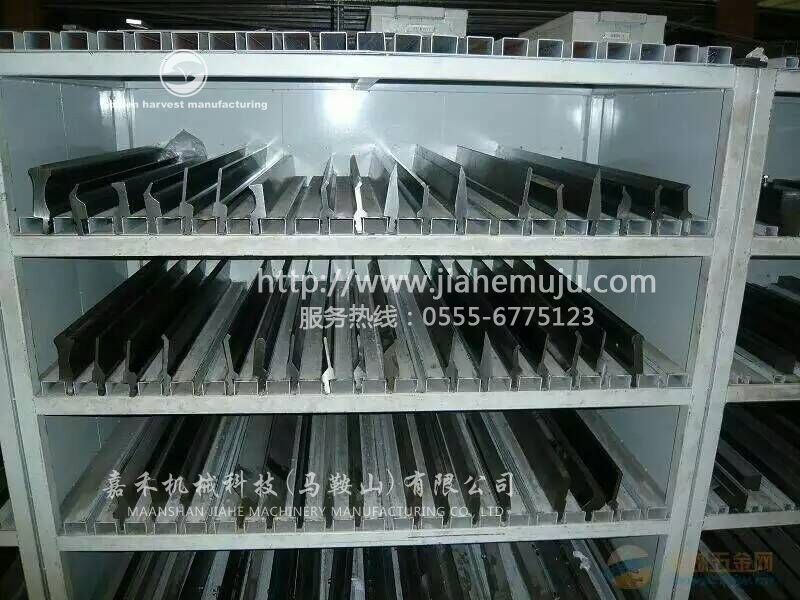
一、精密塑性成形
精密塑性加工技術(shù)在工業(yè)發(fā)達(dá)國(guó)家受到高度重視,并投入大量資金優(yōu)先發(fā)展。70年代美國(guó)空軍主持制訂“鍛造工藝現(xiàn)代化計(jì)劃”,目的是使鍛造這一重要工藝實(shí)現(xiàn)現(xiàn)代化,更多地使用CAD/CAM,使新鍛件的制造周期減少75%。1992年,美國(guó)國(guó)防部提出了“軍用關(guān)鍵技術(shù)清單”,其中包含了等壓成型工藝、數(shù)控計(jì)算機(jī)控制旋壓、塑變和剪切成形機(jī)械、超塑成型/擴(kuò)散連接工藝、液壓延伸成型工藝等精密塑性成型工藝。此外,國(guó)外近年來還發(fā)展了以航空航天產(chǎn)品為應(yīng)用對(duì)象的“大型模鍛件的鍛造及葉片精鍛工藝”、“快速凝固粉末層壓工藝”、“大型復(fù)雜結(jié)構(gòu)件強(qiáng)力旋壓成型工藝”、“難變形材料超塑成形工藝”、“先進(jìn)材料(如金屬基復(fù)合材料、陶瓷基復(fù)合材料等)成形工藝''等。近來,隨著計(jì)算機(jī)和自動(dòng)化技術(shù)對(duì)熱加工成形工藝的滲透,板材成形柔性制造系統(tǒng)也開始嶄露頭角。
二.超塑成形
美國(guó)休斯公司、 BAE公司等在超塑成形技術(shù)方面居世界前列。目前欽合金超塑成形工藝已廣泛用于制造導(dǎo)彈外殼,推進(jìn)劑儲(chǔ)箱,整流罩、球形氣瓶、波紋板及發(fā)動(dòng)機(jī)部件等。鋁合金、鎂合金、鎳基高溫合金、金屬基復(fù)合材料等的超塑成形工藝也在研究。我國(guó)的超塑成形技術(shù)在航天航空及機(jī)械行業(yè)已有應(yīng)用,如航天工業(yè)中的衛(wèi)星部件、導(dǎo)彈和火箭氣瓶等,并采用超塑成形法制造偵察衛(wèi)星的欽合金回收艙。與此同時(shí),還基本上掌握了鋅、銅、鋁、欽合金的超塑成形工藝,最小成形厚度可達(dá)0.3mm,形狀也較復(fù)雜。但壁厚均勻性問題尚待解決。
三.強(qiáng)力旋壓
美國(guó)利用強(qiáng)力旋壓精密配件技術(shù)。已能生產(chǎn)直徑為3.9m、徑向尺寸精度0.05mm、表面粗糙度Ra0.16—0.32μm、壁厚差<0.03mm的導(dǎo)彈殼體。幾乎對(duì)各種金屬均能旋壓成形,且工藝穩(wěn)定,并已實(shí)現(xiàn)設(shè)備大型化,多用途化和自動(dòng)化。錯(cuò)距旋壓、CNC等先進(jìn)旋壓工藝及設(shè)備也已普及使用。
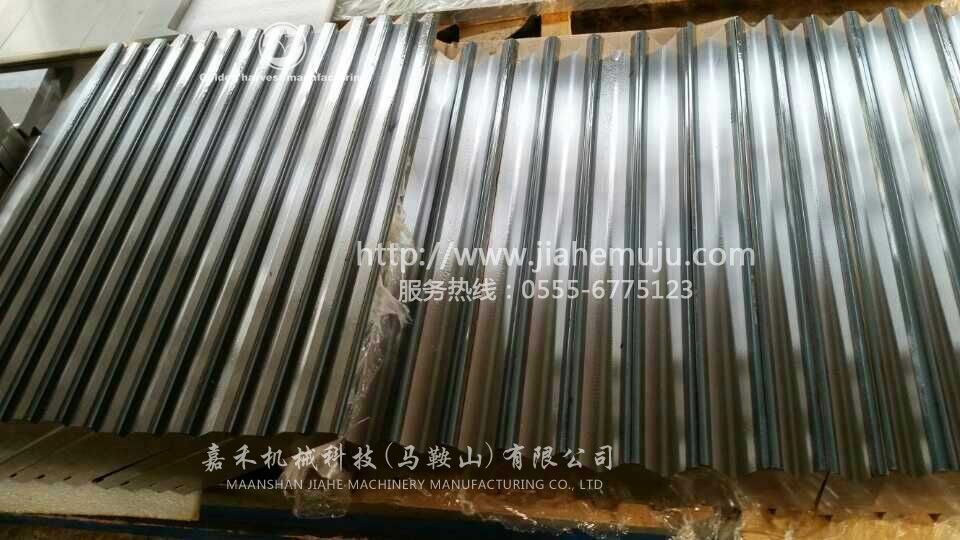
四、精密鑄造
精密鑄造成形工藝不但可以縮短新型武器的研制周期、降低成本,還可以提高武器的靈活性、可靠性。如美國(guó)波音公司生產(chǎn)的巡航導(dǎo)彈的艙體采用鋁合金精密鑄造工藝后,彈體成本降低30%,每枚導(dǎo)彈所需工時(shí)從8000小時(shí)減少到5500小時(shí),且可靠性提高,重量有所降低。
美國(guó)橡樹嶺國(guó)家實(shí)驗(yàn)室、美國(guó)精密鑄造公司和NASA劉易斯研究中心等單位對(duì)A1系金屬間化合物和Ti、
Ni基等特種合金的精密鑄造進(jìn)行了大量研究。他們采用整體一次成形精鑄工藝加工渦噴、渦扇導(dǎo)向器,減少機(jī)加工時(shí)40%,成本降低30%。我國(guó)軍工系統(tǒng)的精密鑄造工藝與國(guó)外相比差距較大。如導(dǎo)彈艙體主要采用低、差壓鑄造法。普通粘土砂鑄型生產(chǎn)艙段,尺寸精度低,表面質(zhì)量較差,內(nèi)部缺陷多,合金液二次氧化嚴(yán)重,力學(xué)性能不高,廢品率高達(dá)20%-30%,目前國(guó)內(nèi)僅能鑄造1.4m以下的艙段。另外象導(dǎo)彈尾翼、飛機(jī)部分器件等仍采用機(jī)械加工方法,不但生產(chǎn)周期長(zhǎng)、成本高,而且可靠性也較差。在特種合金精密鑄造工藝方面,同樣存在很大差距,象單品空心無余量葉片精鑄工藝,在國(guó)外已應(yīng)用于軍工生產(chǎn),而國(guó)內(nèi)尚處于研究階段。至于A1系金屬間化合物的精密鑄造工藝的研究目前還未開。 綜上所述,與國(guó)外相比,我國(guó)在精密鑄造工藝方面約落后10-15年。為了縮短新型武器的研制和生產(chǎn)周期、降低成本、提高可靠性,必須加強(qiáng)精密鑄造工藝的研究。
由于我國(guó)汽車配件制造行業(yè)起步晚、起點(diǎn)低、產(chǎn)業(yè)結(jié)構(gòu)不合理。改革開放以來,汽車配件制造行業(yè)雖有了較快發(fā)展,但與汽車生產(chǎn)大國(guó)相比,差距仍然明顯。特別是與國(guó)外配件制造企業(yè)相比,差距更為明顯。我國(guó)汽車配件制造行業(yè)的差距,除了規(guī)模上的差距,更重要的是制造技術(shù)以及管理技術(shù)上的差距;馬鞍山嘉禾機(jī)械科技有限公司專業(yè)從事折彎模具,數(shù)控折彎模具,生產(chǎn)線配件,精密配件,模具/配件加工,優(yōu)良的設(shè)備,精湛的工藝,嚴(yán)格的檢驗(yàn),完善的售后服務(wù).聯(lián)系電話:18005552119
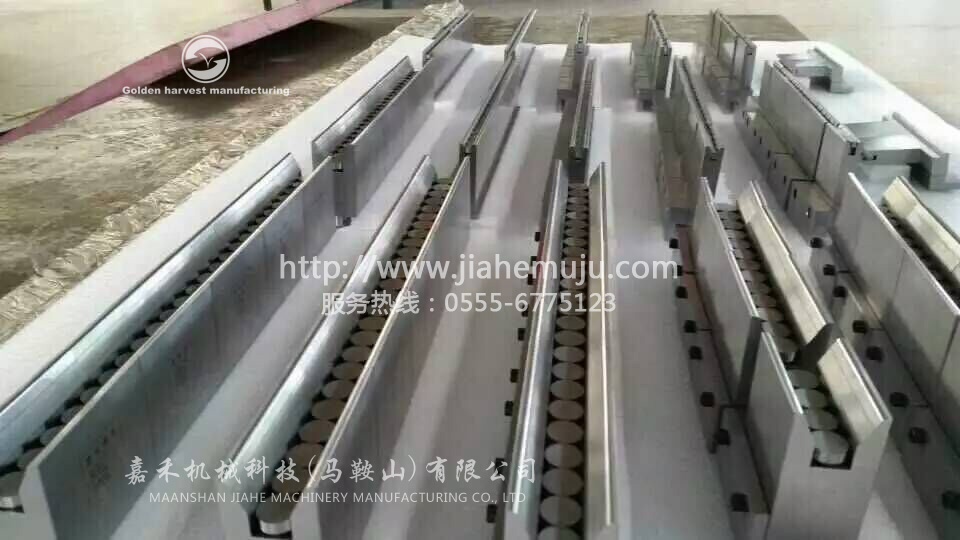